Manufacturing Execution System
Multi-site MES Streamlines FMD’s Microelectronics Development
Germany has made a strong commitment to advancing semiconductor research and development. By establishing the Research Fab Microelectronics Germany (Forschungsfabrik Mikroelektronik Deutschland - FMD) it has brought together 13 research institutes and given them the advantages of a centralized organization.
The move is aimed at making Germany the “world’s most powerful provider for applied research, development, and innovation in the micro and nanoelectronics sector”.
Much of the research undertaken by FMD is aimed at extending semiconductor innovation in directions other than smaller line widths. To further cooperation and accelerated learning among its institutes, FMD decided to source a common Manufacturing Execution System (MES) to operate across its multiple sites. Following a detailed review of such MES systems, FMD selected Critical Manufacturing MES.
The challenge
The institutes within FMD each have their own legacy systems, some of which are ‘home-grown’. Some of these require significant maintenance administration resource. FMD required a new, unified solution that delivered the ability for institutes to work together while offering the flexibility to easily meet the individual needs of different sites.
Dr. Frank Hochschulz, Project Manager, MES Implementation at FMD, says, “We use the same tools and recipes and deploy the same technical processes the industry does, but we’re trying to develop something new. While developing, it’s often not clear what we need to know to get there.”
The workforce comprises many students or new people who are not experienced with the technologies or MES and the fabs’ fabrication cycles can be extremely short, with many iteration cycles of planning and doing for experimentation.
Research institutes have different requirements to typical semiconductor production fabs. There are usually very few materials on the same flow, materials are often processed individually, and it is not uncommon to make one or zero units, used only to take the measurements. The workforce comprises many students or new people who are not experienced with the technologies or MES and the fabs’ fabrication cycles can be extremely short, with many iteration cycles of planning and doing for experimentation.
Manual and ‘on paper’ processes added significant overhead to the research institutes. Alongside better sharing of data and enhanced communication between sites, one of the primary goals for the new MES was to ‘go paperless’.
The project
The MES project, named ‘FMD-Digital’ involves 10 of the 11 FMD institutes with cleanrooms. The new system will see the replacement of legacy MES solutions with a single, modern platform spanning all the sites. Two sites have already deployed the MES, four are in the implementation, and the remaining four are preparing for this digital breakthrough, which will make it easier for the distributed institutes to exchange data and processes and cooperate in technological research.
There was really a lot to learn. When we finished, each of us started working as multipliers in our Institutes.
Dr. Jürgen Grafe, Quality Manager, Fraunhofer IZM (Institute for Reliability and Microintegration) advises on FMD’s approach to the project, “There was really a lot to learn. When we finished, each of us started working as multipliers in our Institutes”
Within the core team are six expert groups dealing with different aspects of the FMD-Digital project.”
- A Work Case Management group analyzed which processes and functionality are needed to manufacture the product.
- A Contamination Management group mapped contamination management of all institutes and a few key industrial partners to define a common strategy across the organization.
- An MES Tool Connection group analyzed which types of tools each institute needed to connect to the MES, with the aim of developing hardware and connection types that could be copied and reused across different sites.
- An Enterprise MES group defined all processes needed to ship materials between institutes and the MES functionality required for this.
- An Implementation and Change Management group worked to align all modelling tasks, MES input requirements, roles, features, tickets and improvements.
- A Process Data and Analysis group defined how to handle process data, with common process analysis tools and solutions for data storage and parsing.
Alongside these expert teams, each institute also has a local project team, including core members responsible for implementing and administering the new MES at their site. The team knew that they needed to configure the MES to meet specific needs of each institute, so system flexibility was crucial.
FMD implemented a pilot site at Fraunhofer IMS (Institute for Microelectronic Circuits and Systems), which had an urgent need for a new MES because of the end of a cooperation with an industry partner who developed a shared MES for the cleanroom. Although MES resources at the site could not be utilized until the partnership had formally ended, FMD and Critical Manufacturing worked together to model the MES and were able to install the new system and return the fab to full productivity within two months.
Naturally, configuration and reconfiguration are also essential, as researchers and students configure the system to handle more of what might go wrong and ensure processes are supported But, around six months after implementation at Fraunhofer IMS, the MES quickly became a commodity and key users were writing new rules and understanding their roles.
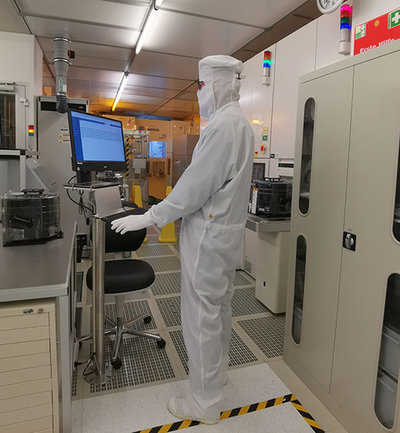
The image is from Fraunhofer IZM (Institute for Reliability and Microintegration) which was the second site to implement some of Critical Manufacturing MES modules. The first module to be implemented here was the maintenance management module which provides the user with checklists, notifications and history features.
Image courtesy: Fraunhofer IZM - Institute for Reliability and Microintegration
With the success of the MES implementation at Fraunhofer IMS, the next site to implement the new MES was Fraunhofer IZM (Institute for Reliability and Microintegration). This site has very different needs, with a more industry-like mode of operation, where some products are manufactured again and again, and is often committed to delivery plans and yield levels. Development focus is on stacking chips and wafers for increased integration depth.
The new MES replaced a home-grown legacy system at IZM. Implementation initially focused on replicating all the functionality of the old system, allowing users to start with familiar functionality.
The goal was for people not to undergo a massive change in material logistics.
IZM commenced productive use of the MES in December 2020. Less than one year later, it started to expand functionality. It adopted the MES’ maintenance management module, which provides users with checklists, notifications and history features. This was followed with the implementation of the system’s planning and scheduling module.
The goal was for people not to undergo a massive change in material logistics. “I was able to model in the Critical Manufacturing product so that our working procedure for a new product or process flow didn’t change – just the modelling. Master data uploaded to the MES makes running the MES very secure. Up to now, we have not lost any production due to wrong processing,” Says Grafe.
The roll out of the MES continues with four more sites in the implementation phase and a target for all remaining institutes to be using the unified system by the end of 2023.
FMD has contracts with some customers that stipulate changes to production cannot be made without first telling them. If this only involves processing of only a few more wafers, an interface between the new and old system is created. Operating at a resource state level, the old system requests resources from the new MES, thereby ensuring a complete picture of current processes and lots is always maintained. The roll out of the MES continues with four more sites in the implementation phase and a target for all remaining institutes to be using the unified system by the end of 2023. Each institute has the freedom and flexibility to decide which MES modules and functionality it needs.
Benefits of the modern MES
The first two institutes, which are fully using the new MES, are seeing multiple benefits. These include a dramatic reduction in manual intervention, which is significantly streamlining processes. The data collected by the MES is available for every function and facilitates more efficient reporting, analysis and communication with other people and processes. Advanced analytics within the MES further help accelerate research and development activities and make it easier for researchers to understand what is happening within processes.
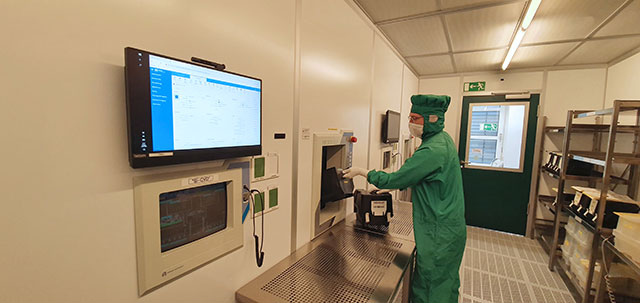
A production process is intricate, with hundreds of steps, services, recipes, checklists, thousands of data collection points, and dozens of parameters. The new system from Critical Manufacturing includes master data management capabilities, allowing all of these parameters to be loaded into the system along with scripts to ensure consistency. (Image courtesy: Forschungsfabrik Mikroelektronik Deutschland - FMD)
The new system provides master data management, which enables complex production flows with hundreds of steps, services, recipes, checklists, thousands of data collections, and dozens of parameters to be loaded into the system with scripts to check for consistency. Shorter flows can be modelled in the MES’ GUI and a master data loader feature enables easier upload of flows for longer runs.
We can now see the flow factor of our lots and materials, so we know exactly how long the processes need and if materials are in the plan.
Materials planning is also more efficient. Grafe says, “We can now see the flow factor of our lots and materials, so we know exactly how long the processes need and if materials are in the plan.”
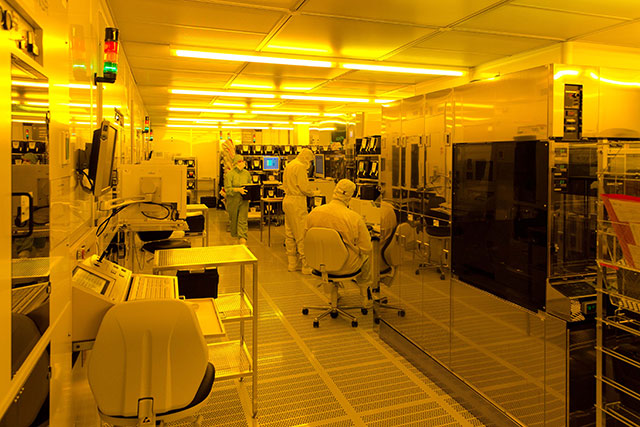
One of the features designed specifically for fabs was chamber-dependent recipes, which enables maintenance technicians to stipulate what a tool is currently capable of doing. It was critical for FMD in order to manage send-ahead wafers efficiently. The MES now provides FMD operators with a clear view of the planned and actual recipe parameters. (Image courtesy: Fraunhofer Institute for Microelectronic Circuits and Systems IMS)
Other features of the system that are specifically designed for fabs include chamber-dependent recipes, which allow maintenance technicians to specify what a tool is currently able to do. The ability to efficiently manage send-ahead wafers is also particularly valuable to FMD, as this process is used extensively. The MES provides operators with the split in planned and actual values and a clear view of planned and actual recipe parameters.
The MES further provides contamination functionality with maintenance, exception and materials management. Having all information in a single system makes it easier to track and manage contamination risks.
FMD realizes performance and resilience benefits from the new system
FMD is delighted with the results it is seeing from the new MES to date.
Grafe comments, “We think with the new MES we can improve our performance regarding planning and resource utilization. We’ve got the tools to investigate that and numbers in the database for reports and analysis.”
Hochschulz concludes, “The common MES project has improved cooperation between the Institutes tremendously. Among other things, we have know-how back-up. Individually, we are not big enough to have admin resources doubled or tripled if someone takes a leave or retires. Now, with a common system, we can call someone else – that’s a major factor for us. We never had that type of backup for these people in the past.”
Further Info: https://www.criticalmanufacturing.com/insights/case-studies/one-mes-for-10-research-institutes/