Sustainability
EMPHASIZING Project
Enhancing Material Properties of recycled glass fibre through Sizing will change the way industry approaches recycled materials.
Whilst the energy industry heads towards decarbonisation, it’s easy to overlook the environmental impacts that decommissioned wind turbine blades leave behind.
Predominantly made of glass fibre, the materials secondary use is currently limited. Separating the glass from the other materials in the blades make-up (wood, aluminium, carbon fibre etc) is uneconomical as the cost of virgin glass is relatively inexpensive – circa €2 per kilo. Unless there is legislation to dictate the use of recycled glass fibre (r-glass), then the business case for the material isn’t currently viable.
Whilst the industry is concentrating on recycling the known and commercially viable materials in the make up of the blades, the non-bio-degradable glass fibre is being buried. This situation cannot continue.
A UK consortium led by B&M Longworth with partners from Ford Motor Company, Gestamp, GEN2PLANK, EMS-Grivory and academic partners from The Welding Institute (TWI) and Brunel University London (BUL) are engaged in a project part funded by Innovate UK to investigate true upcycling of glass fibre to deliver a genuine viable material with high potential secondary use.
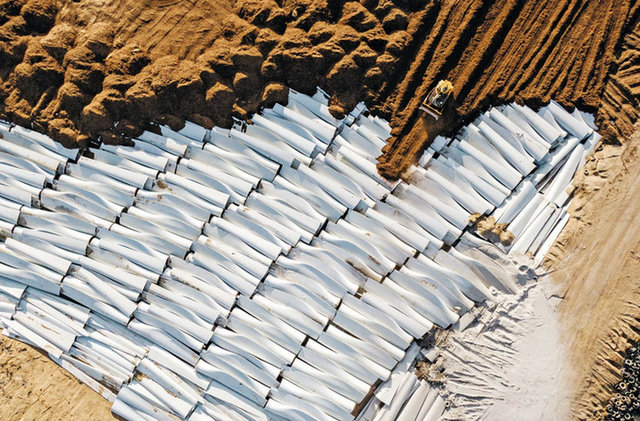
Upcycling of glass fibre
The aim of the project is to develop a material with superior mechanical properties to virgin s-glass but at a price point lower than carbon fibre – providing a viable, commercially acceptable material that can bridge the gap between glass and carbon fibres.
Each blade will be chopped to a size that is commercially acceptable to the secondary use and put through the ‘Pressolysis’ process developed and patented worldwide by B&M Longworth. This process removes the resin using super-heated steam that undergoes compression and decompression cycles to strip the resin from the fibre. Unlike solvolysis or pyrolysis, Pressolysis does not interact with the fibre in any way, thus leaving a pristine fibre. The resin is also recoverable during this process but is not the subject of this project – but is being explored through separate R&D projects. Crucially, the stripping of the resin from the fibre also removes its sizing which allows the upcycling of the fibre as the secondary process.
The aim of the project is to develop a material with superior mechanical properties to virgin s-glass but at a price point lower than carbon fibre – providing a viable, commercially acceptable material that can bridge the gap between glass and carbon fibres.
Marco Hutter, LeMo
Sizing
‘Sizing’ is the term that describes the thin, homogenous coating applied to the surface of fibers during the manufacturing process to protect the filaments during handling, and processing, and also during subsequent compounding and adhesion in composite processing. The project will take advantage of the sizing removal during the Pressolysis process to allow re-sizing of the recovered material.
To upscale and improve the mechanical properties the sizing agent to be applied will be graphene. Graphene is a nano material that is 2D single-layer graphite and is the strongest material known to man. The project will determine the effects of graphene sizing on the mechanical properties of the glass fibre as well as the cost equations of making the material viable for commercial use. The belief among the consortium is that the mechanical properties will be at around the mid-point of glass and carbon fibre with a price point more towards virgin glass fibre.
The project will take advantage of the sizing removal during the Pressolysis process to allow re-sizing of the recovered material.
Marco Hutter, LeMo
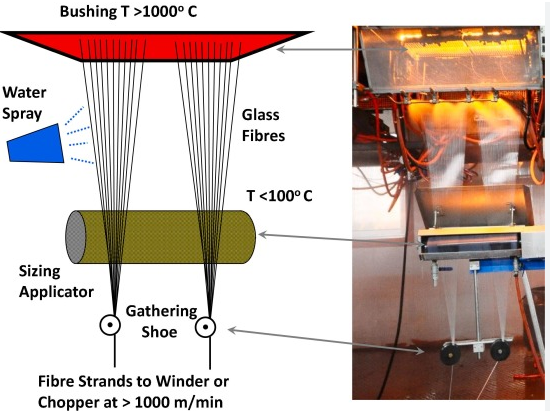
As well as determining the material characteristics of graphene sized glass fibre, a suspension component will be made and tested against its metallic counterpart to assess its suitability for structural parts and to correlate against the CAE predictions.
The final element of the project will be to understand the life-cycle analysis for Scopes 1 & 2 – material production and manufacturing phase – as well as Scope 3 for the weight reduction of the component on the vehicle in the use phase. The Scope 1 data will include the CO2 output from the Pressolysis process to ensure the full emissions are taken into account.
It is the responsibility of the industry to ensure that we can find ways of using discarded materials responsibly in a way that enhances the business case.
Marco Hutter, LeMo
Due to finish in October 2024, the aims of the project are clear and will ensure that there is a known business case for utilising upcycled glass fibre. We live in a world of unprecedented climate change and it is the responsibility of the industry to ensure that we can find ways of using discarded materials responsibly in a way that enhances the business case. Once there is legislation to prevent glass fibre going into landfill, the whole of the industry will be obliged to recycle at any cost which is potentially damaging to the existing supply chain.
Avoiding this scenario is where the EMPHASING project comes into its own. Enhancing Material Properties of recycled glass fibre through Sizing will change the way industry approaches recycled materials.
Dr. Alan Banks
BEng (Hons), MSc, PhD, CEng, MSAE, FIKE, FIET
Chairman – Composites UK