Feature construction
Arthur Mamou-Mani
a nd the next generation of architecture
What truly lies ahead for architecture in the era of artificial intelligence and robotics? Lucy Ingham hears from pioneering architect Arthur Mamou-Mani to find out how algorithmic design and robotic construction could play vital roles in building projects of the future.
In every generation of architects, there are a handful whose work truly lays the foundations for the next era of the field. Arthur Mamou-Mani, director of Mamou-Mani, is one such architect, whose pioneering work in digital design and construction is at a level few of his contemporaries can match.
With a client list that includes ARUP, Buro Happold Engineering, fashion house Karen Millen and the Burning Man Festival, and an impressive list of awards since founding his practice in 2011, Mamou-Mani has gained a reputation for innovative design and fabrication techniques and striking temporary structures.
However, despite qualifying from the prestigious Architectural Association School of Architecture (AA) and running his own RIBA chartered practice, Mamou-Mani has had to contend with claims that he is not a true architect.
“A lot of times I was told 'you're not an architect' and that hurt me a little bit, but I accept it now,” says Mamou-Mani at an RIBA-backed CPD session at London’s designjunction. “I think I went beyond architecture, but I always end up going back to it.”
One reason for this response from his contemporaries is that few architects also run digital fabrication labs. Mamou-Mani does, however, in the form of FabPub, where many of the innovative structures and forms his studio is known for are created using large-scale 3D printers and laser cutters.
“FabPub is our fabricaion lab where people all around the place come and use our machines and so I strongly believe in complementarity in businesses,” he says. “Mamou-Mani is the studio but really without the machines at FabPub we are not able to do any of that, and I think without Mamou-Mani people wouldn't necessarily go to FabPub.”
This expertise, combined with a use of algorithmic modeling tools such as Grasshopper, has allowed Mamou-Mani to create remarkable structures, many of which are temporary, such as his work for Burning Man, which is burned as part of the festival.
“I think the fact that we are not afraid to build temporary structures is a bit of an unconventional thing for an architect who is used to permenance, and that has informed a lot of the projects that came after,” he explains. “In fact, each project is designed with that idea of temporarity, of preciousness, of experience.”
However, while much of Mamou-Mani’s work thus far has been relatively temporary, he is increasingly moving into larger and more permanent structures, and significantly innovating in construction in the process. And it is this work that may well prove to be the foundation of a whole new approach to architecture and construction.
Much of Mamou-Mani’s work has been designed to be temporary, such as this structure, Tangential Dreams, which was burned at the Burning Man festival. Photography by Reagan Parrish.
Using algorithms in design: keeping the story in parametric architecture
At the heart of much of Mamou-Mani’s work is the use of algorithmic design, using a method known as parametric architecture, an evolving field that he has been involved with since the early days of his career. Central to this is the design tool Grasshopper, but in the early days he worked with an arguably more rudimentary parametric design tool: GenerativeComponents.
“When I graduated, at the time at the AA there was a tool that we used very similar to Grasshopper called GenerativeComponents, and it allowed us to generate things in relation to parameters, in this case environmental parameters,” he explains.
“It generated a graph, a sort of mind map of what's going on inside this component, and it allowed you to see architecture of design not as an end thing that you sculpt, but as a system, which is why we called it parametric design in the field because it allows you to change parameters and think of geometries as almost like a DNA that creates a multiplicity of projects.”
“
I don't think people can relate to
parametric architecture unless there is something poetic about it.Using such tools, Mamou-Mani has produced a host of remarkable designs, from popup structures and pavilions to interior structures, such as wall panels and window displays. However, what unites them is a deeply organic, almost otherworldly feel.
This year, for example, he will produce the main temple at Burning Man, a spiraling structure made of timber trusses that converge in a central point holding a giant 3D printed mandala. And while the structure is striking in form, it is also highly functional, creating quiet alcoves set back from the main path into the central space.
Designed with the parametric tool Grasshopper, the temple, Galaxia, is an excellent showcase of the new design language this approach introduces, however Mamou-Mani is keen to stress that a human touch remains essential to good parametric design.
“I don't think people can relate to parametric architecture unless there is something poetic about it, and I don't think the science or the scientific aspect of things really talks to people,” he explains.
“That's why I think it's really important to keep a story, and that story emerges from it looking like something, and I think everyone can see something in forms and it’s for us as architects – the machines won't do that – it’s for us to see that opportunity.”
The Polibot, a robotic construction tool developed by Mamou-Mani, on display at ARUP.
Beyond 3D printing: robotic construction
While many of Mamou-Mani’s projects involve 3D printing, he is not convinced by the additive manufacturing approach that many are predicting for the construction of houses and other similar structures.
“I think with 3D printing there are so many attempts to do homes, 3D printing the first home. I don't think that there's a place that someone lives in that has been 3D printed, I think there are conceptual ones,” he says.
“I'm not sure that extruding in concrete for I don't know how much time to create a building is the solution. I think we've been so used to working with different kinds of materials: timber, bricks, stone, that suddenly extruding plastic, which means not only revolutionising the machines that build it but also the material is so much revolution that it's going to be a bit longer.”
Instead, he has been integral to the development of an alternative approach to digitised construction, which in its current early form is being showcased in ARUP’s head office in London.
“
In its showcase at ARUP, the Polibot picks up materials and places them piece by piece to form a tower, before dismantling it and starting again.
“I got in touch with ARUP, they do a competition every year to promote young designers in their atrium, and we suggested to build not the design, but to build the machine around the design, the machine that creates the design,” he explains.
“We've always used digitial fabrication tools in our studio, but we're always limited to that kind of scale and that kind of material – plastic mainly, or wood, but in the form of subtractive technology, not additive – so the solution, I think, would be in between a spidercam and a 3D printer: it's called a cable robot, in this case we called it the Polibot.”
In its showcase at ARUP, the Polibot picks up materials and places them piece by piece to form a tower, before dismantling it and starting again. A one-of-a-kind construction tool, it was created entirely by Mamou-Mani and his colleagues using a combination of 3D printing and laser-cutting, and is equipped with 3D vision using an off-the-shelf Microsoft Kinect.
“It's a crane. It's really just a crane, but it's a robotically controlled crane so it allows people like us that are trained in digital fabrication to scale up to buildings, and really I think that's the biggest challenge, at least for me, is scaling up to the building scale,” explains Mamou-Mani.
“Because of its complexity, because of what we're building and the tolerances, it has what's called a feedback loop, it goes and reads itself and autocorrects when there is a problem. So I really hope this will mean the future of construction.”
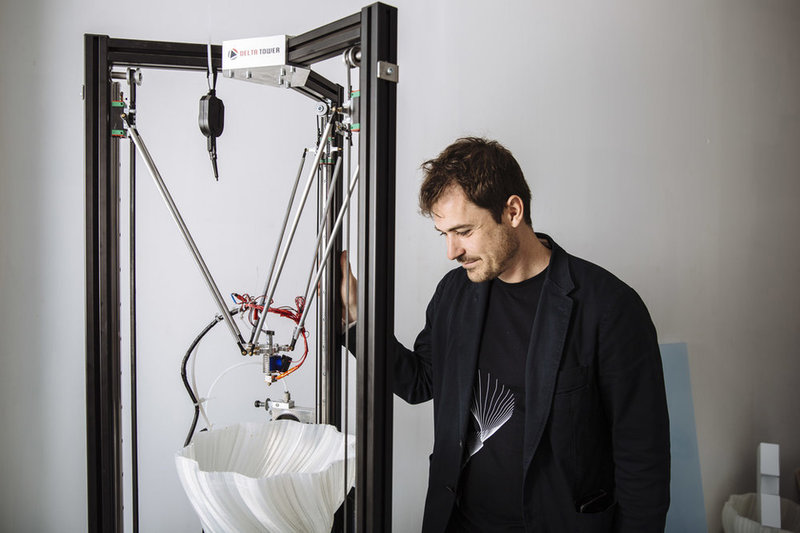
Arthur Mamou-Mani is pioneering new construction techniques.
At present the robot is neither large enough, nor working at the level of granular detail that would be required, for it to construct complex, full-scale buildings. However, it is impressive for such an early version, and clearly has the potential to develop into a full-scale tool for construction with adequate time and refinement.
“I think there's still a tolerance of around 2cm, plus or minus, which is ok because the timber pieces, they expand on both sides, so even if its 2cm in or out it doesn't create a massive problem. What’s really, really important now, especially at that scale, is the idea of machine learning and self-correction and feedback loops,” he says.
“Because we're sending the information from Grasshopper directly to the robot, we can establish a kind of feedback loop with things like Kinect and so the Grasshopper will read that the piece hasn't been picked at the right spot or its slightly off, so we can tell the computer to autocorrect the code and then place it at the right spot.
“But it still requires really precise 3D scanning, and I think that technology is not yet completely affordable. The Kinect is the closest we can get to a precise thing, but it's still a massive challenge.”
This, however, hasn’t stopped Mamou-Mani from looking at how the tool can be used to construct a full-scale building. He had hoped to use the Polibot to build London’s Holocaust Memorial, which Mamou-Mani’s algorithmic design was shortlisted for, but ultimately the firm lost out to David Adjaye and Ron Arad.
Nevertheless, the idea attracted considerable support, particularly from the project’s structural engineer Francis Archer, and so it is likely to be only a matter of time before the construction robot finds its first full-scale project.
“He pushed that robot as well because he also thinks that it will have an impact on the construction industry,” says Mamou-Mani of Archer.
The shortlisted design for the Holocaust Memorial in London, which Mamou-Mani had planned to build using his construction robot. Architect: Heneghan Peng, computational designers: Mamou-Mani.
Transforming architecture: Mamou-Mani’s vision
While much of Mamou-Mani’s work has a distinct touch of automation about it, he is very confident about the role of humans in future architecture.
“We work with machines, and when I say with them it means that all their constraints and all their limitations are actually opportunities,” he says. “I know it sounds weird, but I don't believe that machines will take over from us. On the contrary: they'll be friends that we'll work alongside.”
However, he does see the growing presence of the digital reshaping what it means to be an architect, transforming it into a role more reminiscent of days long passed.
“I really, really believe that the separation between engineers, contractors, designers, jewellery designers, you name it, will be broken when it comes to machines that will build projects, when it comes to working with digital fabrication and tool software that allows you to connect the different skills,” he says. “I think we'll see a lot of the profession merging, and we'll see a return to what I call the master builders, which is the people that build the cathedrals and were able to test their design straight away as they were designing it, building it.”
“
I think we'll see a lot of the profession merging, and we'll see a return to what I call the master builders.”
As part of this, he also believes that architecture students should be encouraged to think entrepreneurially as well as structurally.
“As well as the revolution of digital fabrication and open-source software, I also think that entrepreneurship is something that is not really being taught in architecture school, and I really, really believe in it,” he says.
“I believe the students should be taught how to finance their project, how to organise them and how to think of logistics, think in four dimensions. And that's why we raise funds; you'll always see us on Kickstarter doing something.”
Mamou-Mani’s design for Burning Man 2018, Galaxia, was selected as the main temple for the festival. All images courtesy of Mamou-Mani.
Lucy Ingham is the editor of
architecture and construction magazine Design & Build Review, where this article was originally published.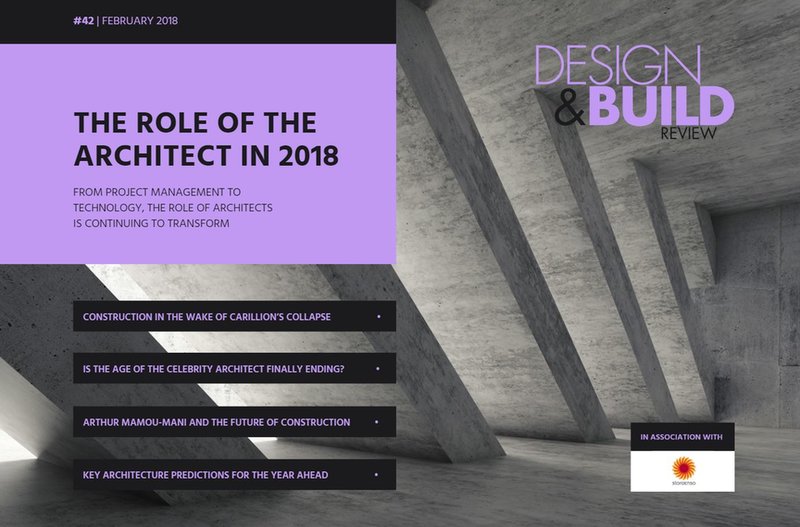